ISO P-type workpiece materials include metal materials commonly referred to as steel. Although steel does not exhibit significant machining challenges at the material level (such as heat-resistant aerospace alloys used in the aerospace industry), alloy steel and iron are the most widely used workpiece materials in a wide range of industries. Such a wide range of uses has led to the development of a wide variety of alloy steels with different physical properties, which has created various metal cutting performance problems. In addition to the economic considerations required for mass production, these issues also make the processing of ISO P-type steel parts a major challenge for parts manufacturers and tool manufacturers of these parts.
ISO system
The ISO metalworking workpiece material classification system is divided into six categories. Class K includes cast iron. Heat resistant superalloys such as nickel-based and titanium-based alloys belong to the S category. Class H materials are characterized by hardness and consist essentially of steel with a hardness of 45-65 HRc. Stainless steel (alloy steel with a chromium content greater than 12%) constitutes Class M. Class N contains non-ferrous metals, mainly aluminum, copper and brass. Finally, the P category consists of carbon steel, low alloy steel and high alloy steel, including alloy steel with a hardness of up to 400HB and stainless steel with a chromium content of no more than 12%. Some long swarf malleable cast irons are also classified as ISO P.
The above classification is basically based on the main physical properties of different materials. These properties essentially determine the material's processing performance and its impact on cutting. Class K metals are characterized by abrasiveness, which accelerates tool wear. S class heat resistant superalloys generally poor thermal conductivity, which can lead to heat the polyethylene product of the cutting zone cutting tool modification. The hardness of Class H metals not only creates a lot of pressure on the tool, but also generates heat. M strain hardening type having characteristics of the workpiece material in the cutting process will harden with the deformation. Cutting pressure and heat will cause an increase in notch wear and other problems. Class N metals exhibit a tendency to stick to the cutting tool, causing built-up edges, poor surface quality, and fracture of the cutting tool.
Since the above five types of ISO materials have more or less one main physical property, the cutting tool can be designed to eliminate the adverse effects of its properties on the cutting tool to some extent. For example, the tool used for cutting H based material generally requires a higher strength, and metal cutting tool more N sharp increase, and facilitates the formation of designs using the chip flow so as to minimize the risk of sticking of the cutting edge.
However, ISO P class artifacts present more complex challenges. Steels, especially the vastly different alloy steels, often exhibit more than one or even all properties that affect the performance of the cutting tool, although usually not extreme. This poses a problem for the development of the tool; for example, in many cases, a sharp edge tool designed to cope with the tendency of low alloy steel to stick may not be able to withstand the abrasive properties of another steel component. In addition, as manufacturers pursue materials that match the specific performance needs of customer parts, the development of various specialty alloy steels continues to grow.
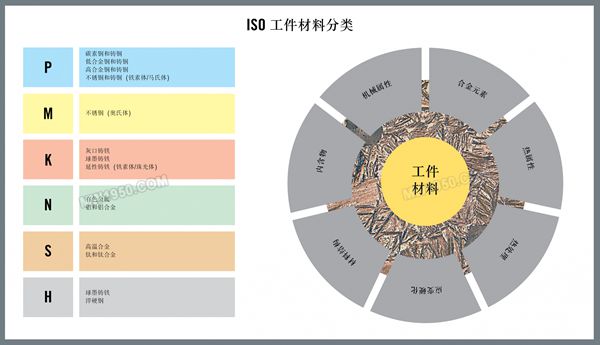
Understanding metal cutting
When machining alloy steel, how to efficiently balance the various performance properties of the tool is like dancing on a steel wire. To achieve this balance, you need to understand the nature of metal cutting and the interaction between the workpiece material and the cutting tool.
Metal cutting is not a cleaving process similar to the knife cutting method, but a process of applying pressure to the workpiece material until it is deformed and cut in the form of chips. The shearing operation is accompanied by a number of additional effects. The mechanical forces required to fully deform the material create high pressures and high heat, resulting in temperatures reaching the 800-900 °C level. Intermittent cutting or machining of parts with hard inclusions can cause the cutting tool to be impacted. In addition to mechanical factors, high temperatures and pressures also catalyze chemical reactions between the cutting material and the workpiece material, resulting in chemical wear in the form of diffusion or crater. Last but not least, metal cutting produces intense friction. Since the cutting process forms chips and rubs on the tool, friction is generated, which is called the frictional effect; tribology is the science of studying the surfaces in contact with each other at a certain temperature and pressure and measuring the degree of mutual change of these surfaces. All of these forces and interactions produce different results; perhaps the most important result is tool wear.
Different steel parts use different tools
The influence of the machining process on the steel parts depends on the alloy steel composition and the manufacturing process of the steel parts. For example, carbon steel with a carbon content of less than 0.25% is used in applications such as automotive axles that require high strength, impact resistance, and fracture resistance. Rolled or forged alloy steels can produce chips that are difficult to break, which can scratch the surface of the tool and cause crater wear and even sticking problems. For these components, the cutting tool design has a sharp edge for more efficient shearing of the workpiece material while the coating resists chemical wear and provides lubrication to the cutting surface.
On the other hand, high-alloy steels with alloys (including elements such as manganese) exceeding 5% can be hardened to produce parts that require wear resistance and rigidity, such as hydraulic parts and machine parts. Usually the chips produced are easy to form and break, but the tools that process these alloys are subject to high pressures and temperatures. For unmachined workpieces produced by casting or forging processes, the hard surface and the contents that may come from the mold may require the cutting tool to have both toughness and abrasion resistance.
Example of a blade designed for steel turning: WNMG080404-MF2, TP1500
Example of a blade designed for steel milling: LOEX080404TR-M08, F40M
economic factors
The traditional goal of machining operations is to produce more parts at a faster rate, so the most aggressive cutting parameters need to be used whenever possible. However, other issues will limit this simple goal. Economic factors play a key role in the selection of cutting parameters. Parts such as aerospace components made from specialty alloys have relatively low yields in most cases. Manufacturers process parts at this speed to maximize process reliability, protect expensive workpiece materials, and invest in valuable manufacturing time. Therefore, the processing speed and feed rate used by advanced workpiece materials are generally efficient but relatively conservative.
Steel processing methods often vary. Many steel parts require high volume production and are required to be completed as quickly as possible in order to process relatively simple parts with low cost workpiece materials for maximum economic return. Increasing the cutting speed usually increases productivity, but this requires the cutting tool's substrate to maintain high strength at high cutting temperatures. Given the increasing variety of alloy steels, it is necessary for the manufacturer or machine shop to consult the tool manufacturer to determine the tool grade and geometry that best suits a particular application. The current tool development is aimed at producing tools that can solve a variety of machining problems in alloy steel. Manufacturers are looking for sharper and stronger tools and can overcome thermal, pressure, chemical and adhesive wear problems through coatings and grooves.
envirnmental factor
Environmental factors are a factor that manufacturers have only considered in recent years, and they also affect the choice of processing parameters for steel materials. Many manufacturers are now focusing on environmentally conscious or “green†processing initiatives. These include reducing energy consumption and minimizing waste from processing. Although technical challenges remain a major issue in the processing of specialty metals, the importance of environmental factors in processing steel is becoming increasingly prominent.
One way to reduce energy consumption is to reduce the cutting speed. In many cases, manufacturers can maintain productivity by proportionally increasing feed rates and depth of cut. In addition to saving energy, this strategy also extends tool life. This, in turn, reduces the waste stream produced by the process, as producing the same number of parts consumes less cutting edges and "run and throw" blades. Reducing the cutting speed also reduces heat generation, which reduces the need for metalworking coolants , as the coolant itself becomes a waste that is not required for metal processing.
in conclusion
Since ISO P steels are well known and widely used in the manufacture of conventional parts, the processing of alloy steels is usually not closely followed and analyzed in detail. However, if manufacturers understand that many of the machining challenges of steel can be eliminated by careful selection of tools, even small improvements in the productivity of high-volume parts can significantly improve profitability and even benefit the environment. .
DC Axial Fan 80x80x38,12v DC Axial Fan,8038 24v 02a Dc Fan,8038 Axial Cooling Fan
Crown Electronics CO., LTD , https://www.crownelectronicstw.com