1 Overview
The negative pressure lost mold vacuum sand box originally used in our factory is a supporting foaming equipment product of a factory in Shandong. The vent hole of the vacuum part is covered with a thin filter and fixed with a few screws. . In the case of molding casting, the filter screen is easily damaged due to long-time baking of high-temperature molten steel and high-temperature molding sand, so that the molding sand passes through the damaged filter screen and enters the suction passage to cause blockage during vacuuming, thereby making the sand box The degree of vacuum drops and the negative pressure is insufficient.
Due to the lack of vacuum in the sandbox, the problem of casting defects has attracted the attention of our engineers and technicians. After repeated trials and tests, we have carried out a series of technical transformations on the vacuum flask to finally solve the problem of insufficient vacuum. .
2. The purpose and function of negative pressure die casting vacuuming
After the white mold is made, it is dried in the sand box and evenly layered with dry sand to form a compact shape. Then the air between the sand grains in the sand box is pumped away by the vacuum pump, so that the sand type in the sealed sand box has a certain shape. The compaction degree is carried out under the negative pressure state to accelerate the exhaust speed and increase the displacement, reduce the air pressure between the metal and the pattern, accelerate the advancement speed of the metal liquid stream front, and improve the filling ability of the casting. It is beneficial to reduce the carbon black defects on the surface of the casting; vacuuming can also inhibit the burning of white mold materials, promote vaporization, improve the environment, reduce pollution to the atmosphere; increase the fluidity and formability of the metal liquid stream, and make the contour of the casting clearer.
3. Casting defects caused by insufficient vacuum
(1) The main reason for the collapse of the box is that the vacuum in the flask is too low, the height is uneven, and the vacuum is drastically reduced. One of the reasons for the lack of vacuum in the negative pressure of the flask is that the gauze and the suction line are blocked, so that the pumping capacity is lowered and the degree of vacuum is lowered.
(2) When the white mold (EPC module) is in contact with the high-temperature metal liquid stream, it is decomposed into gaseous, liquid and solid components. Under high temperature heat conditions, 46% of the EPC white mold decomposes to a gaseous state and a solid state. 54% of the EPC white molds are not completely decomposed until the casting is completed, and exist in the liquid phase state at the boundary of the mold before vaporization. In order to completely vaporize the liquid, it is necessary to have a certain time and sufficient temperature, and these liquid EPC film layers are contracted by their own surface tension to form a discontinuous stripe shape, that is, a wrinkle defect. Also, because the degree of vacuum is insufficient, the suction force is too small, and the EPC tar-like liquid substance is not sucked into the molding sand through the gap of the coating layer to promote the formation of wrinkles.
(3) Porosity The pore is a void distributed on the surface or section of the casting. The EPC white mold is decomposed into solid, liquid and gaseous substances by the thermal action of the high temperature metal liquid stream. A large amount of gas is not pumped away by the vacuum pump through the suction passage of the flask, or the vacuum is too small, and the vacuum capacity is insufficient, resulting in gas. Stuck in the casting to create pores.
4. Negative pressure vacuum flask without filter network transformation plan
(1) The bottom of the original sand box before the reformation of the air pump at the bottom of the sand box is double-layered. The steel plate on the surface is drilled with many vent holes with a diameter of 10mm. The hole is covered with a layer of 100 mesh (mesh diameter 0.154mm). The stainless steel gauze is covered, and the gauze is bolted by several pressure plates, as shown in Figure 1, and the physical object is shown in Figure 2.
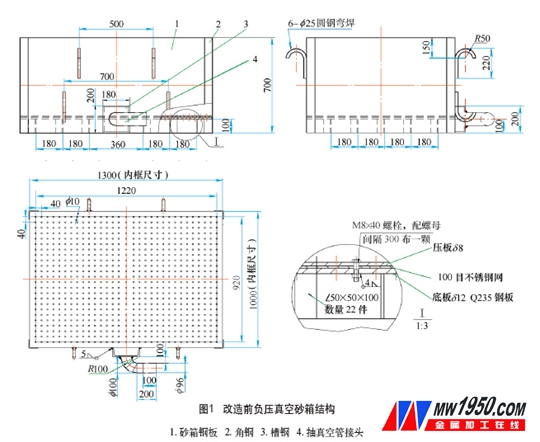
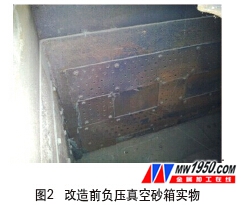
After the transformation, the vent hole is replaced by 5# angle steel, and the welding is carried out in sections with the bottom plate. The welding length of each welding seam is 50mm, the weld spacing is 100mm, and the welding gap is 1~1.5mm. That is, when welding, some manual steel saw blades are put into the welding. After taking it out, it is taken out to form an air gap channel. The spacing between each angle is 200mm, evenly distributed throughout the bottom of the flask. The bottom layer is only designed with a single layer structure, the angle steel vent hole is connected with the outer suction passage, and the outer suction passage around the sand box is made of 10# channel steel. The weld seam of the channel steel and the outer steel plate of the flask is full weld, and welding is ensured. Quality, can not have pores, slag inclusions, welding tumors and other welding defects, otherwise it will affect the airtightness of the sand box, so that the vacuum is insufficient. The modified sand box structure is shown in Figure 3, and the physical object is shown in Figure 4.
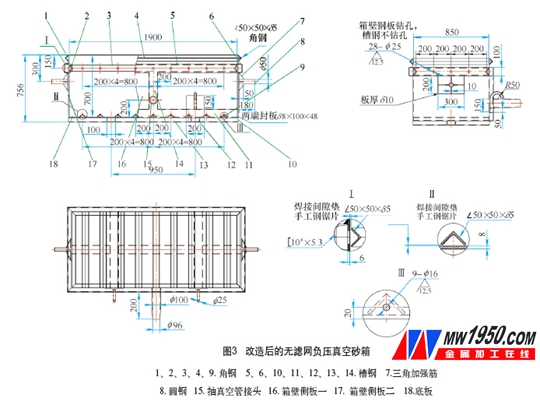
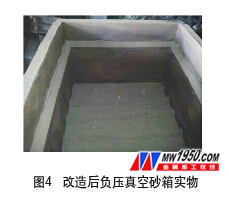
(2) Design of the suction passage around the upper part of the sand box In order to increase the vacuum pressure on the upper part of the sand box, we use the 5# angle steel to weld the suction passage on the inner side of the upper part of the sand box, which is the same as the bottom angle steel. The welding method is made by section welding of the method. The outer side of the sand box is also welded with the exhaust passage of the 10# channel steel and connected to the inner air passage, and penetrates with the bottom suction passage to form a pumping communication system. In this way, the upper part and the bottom part of the whole sand box can maintain a certain degree of vacuum, thereby maintaining the overall mold vacuum degree tends to be stable, and ensuring that the casting piece is not scrapped when the pouring is caused.
(3) Reconstruction of the vacuum tube joint The bottom of the original sand box has a double-layer structure, so the vacuum tube joint needs to be bent through the sand box at a 90° connection, which not only increases the air resistance, but also makes the vacuum pump power insufficiently insufficient, resulting in a vacuum. Degree drops. The bottom of the sand box is designed as a single-layer structure, and the vacuum tube joint is changed to the vertical vertical sand box connection. There is no bending phenomenon, the air resistance is greatly reduced, the pumping vacuum strength is obviously enhanced, and the vacuum pressure of the sand box is significantly improved. .
5. The effect achieved
After the modified sand box is put into production, more than a dozen boxes of castings are poured. Compared with the sand box with the filter screen, the suction gas strength is greatly improved when the sand box without the filter mesh is poured, and the vacuum degree is stable. There was no collapse, the quality of the castings improved significantly, and the sandbox transformation was a complete success. The quality of the comparative castings of the sand box castings before and after the transformation of the five groups is selected, see attached table.
6. Conclusion
In short, in the vacuum die casting of lost foam, the lack of vacuum will cause casting quality problems. In the production practice, we must be good at observation, analyze various reasons, prescribe the right medicine and boldly propose the transformation plan, and implement the transformation measures, so that the qualified castings can be poured and the best effect can be achieved. Practice has proved that it is feasible to use angle steel instead of filter screen as the pumping passage. The sand box is durable and the cost of materials is not high. It is worthy of popularization and application.
About the author: Liang Yuxing, a mechanical plant of Guangxi Youjiang Mining Bureau, an engineer, mainly engaged in mechanical design work.
Single Handle Faucets
The present invention provides a multifunctional pull faucet, comprising: a faucet body, a drawing part is provided at the water outlet port thereof, and the drawing part is connected to a main channel, wherein at least three are provided in the faucet body A branch channel, and the three branch channels are all connected to the main channel. A multifunctional pull faucet provided by the present invention, wherein the hot water channel, the cold water channel and the water purification channel (pure water channel) are all connected to the main channel , And the main channel is connected with the drawing part on the main body of the faucet, so that the drawing part can obtain the water quality (hot water, cold water, purified water or pure water) required by different users, thereby improving the user experience, and , By integrating the hot water channel, cold water channel and pure water channel (pure water channel) into the main channel, the internal structure of the faucet is simplified, and the production cost of the faucet is reduced..
Single Handle Faucets,Pull Out Laundry Faucet,Pull Out Shower Handle,Stainless Steel Single Handle Faucets
Yuyao Zelin Sanitary Ware Co., Ltd , https://www.zelinshower.com