Abstract : The traditional crankshaft deep inclined oil hole processing method has many disadvantages such as process dispersion, high processing cost and large coolant consumption. Now high-speed horizontal machining center is used to ensure process concentration, and advanced tool micro-lubrication is applied (MinimalQuantityLu. ..
Abstract: The traditional deep crank oil hole machining method has many disadvantages such as process dispersion, high processing cost and large coolant consumption. High-speed horizontal machining center is used to ensure process concentration and advanced tool micro-lubrication (Minimal Quantity Lubrication) , MQL) processing technology, to achieve the technical breakthrough of crankshaft deep oblique oil hole processing, to achieve quality, efficiency, environmental protection and low cost production goals, in line with the green sustainable development. Through the actual processing of the deep-sloping oil hole of the crankshaft, the composition and use conditions of the MQL are deeply studied. Key words: crankshaft; deep oblique oil hole; micro lubrication processing
0 Introduction Crankshaft deep oblique oil å‘L machining is one of the difficulties in crankshaft machining. In addition to the characteristics of deep hole machining, it also has a multi-angle distribution of space between the hole and the hole, and the size, shape and rigidity of each section are different. It brings great difficulty to the process of positioning, clamping, drilling and cooling.
Domestic automobile manufacturers processing the deep-sloping oil holes of the crankshaft mostly adopt the following two traditional processing methods: 1) pass (special) machine + twist drill tool, graded feed processing, water cooling tool; 2) special machine + gun drill, guide bush Guided, high pressure water (oil) lubricates the cooling tool.
The above processing technology, process dispersion, more parallel equipment, large floor space, low efficiency, high investment costs, and sewage (oil) recovery is more difficult. In view of the above problems, the horizontal high-speed machining center machine tool can be used, and the process concentration scheme is adopted, and the micro-lubrication technology is applied, that is, the micro-cutting oil is mixed with the compressed air having a certain pressure and atomized, and sprayed to the cutting area to the cutter and The chip and the tool-to-workpiece interface are effectively lubricated to reduce friction and prevent chips from sticking to the tool, while also cooling the processing area and facilitating chip evacuation, which significantly improves the machining conditions.
1. Crankshaft of the tool micro-lubrication technology 1.1 Crankshaft parameters Figure 1 shows the appearance of the crankshaft deep oblique oil hole. The crankshaft material is S30CMS1; the hardness is 78-87HRD.
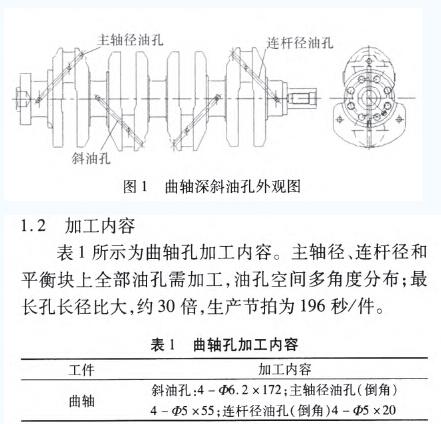
1.3 New process plan The new process plan equipment uses high-speed horizontal machining center, the process concentrates and applies advanced tool micro-lubrication technology, and configures special tools. For deep oil holes with large long diameter, it is continuous in processing. Feed cutting, improve machining efficiency, reduce the use of cutting fluid, and achieve clean production.
2, the main research content and application of the project MQL technology is mixed in the compressed air micron (oil mist radius <20txm) pollution-free oil mist, in the horizontal machining center through the inside of the spindle and the tool å‘L spray to the cutting area, Instead of a large amount of cutting fluid, the cooling of the cutting point is performed. The high-speed supply of fog particles increases the permeability of the lubricant, which reduces the friction between the tool and the workpiece, improves the tool life and the quality of the machined surface, and avoids the quenching effect caused by the conventional water cooling. The appropriate high-speed machining causes the fracture point of the cutting layer to appear in advance. If measures are taken in time to keep the iron filings at a high temperature away from the tip, the tool is protected. Since the amount of lubricating oil is only one ten-thousandth of the amount of conventional cutting fluid, the cost of the coolant is greatly reduced, and the site use and energy demand are reduced! Keep the tools, workpieces and chips outside the cutting area dry, avoiding the problem of dealing with waste liquid, and more in line with the green sustainable development.
2.1 Oil mist transport channel After the particulate oil mist is mixed with the compressed air, it reaches the cutting zone through a certain passage, and the passage is required to be smooth, minimize the blind zone and eddy current, and prevent the oil mist from solidifying. In the horizontal high-speed machining center, the main shaft channel has a built-in single channel. Therefore, MQL technology is required to have a separate micro-generation device to pulverize the oil and gas mixture into fine particles, which are then sent to the main shaft channel by compressed air. Figure 2 shows the oil mist transportation. Schematic diagram of the channel, the oil and gas mixture enters the inner hole of the rod installed in the main shaft through the MQL special tube, ball valve and hose, and finally reaches the front cone surface of the spindle mounting shank.
Figure 2 Schematic diagram of the oil mist transport channel
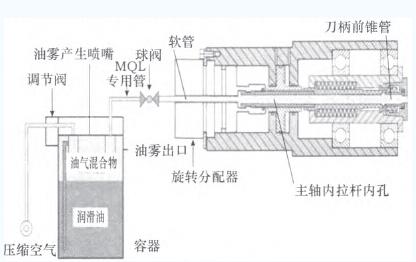
2.2 gas source As a carrier for transporting particulate oil mist, compressed air must have a certain pressure, the pressure range is o. 5~0.8MPa, the pressure value is related to the length of the channel, and is adjusted according to the cutting condition. At the same time, the clean air itself has high cleanliness. Excessive moisture and impurities will affect the atomization effect of the particulate oil mist, and reduce the tool outlet oil. The proportion of fog causes insufficient lubrication during tool processing, which directly affects tool life and processing quality. Therefore, the specific measures use industrial compressed gas through filters, oil-water separators and booster pumps. The filtration accuracy is 5txm, and then enter the MQL generating device. . 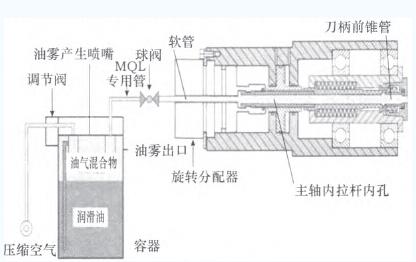
2.3 Tools and Auxiliary Tools The specific requirements for tools and auxiliary tools are as follows: 1) The joint between the tool and the auxiliary device must be specially treated to ensure that the end face of the knife accessory is in close contact. 2) The tool should have excellent high temperature resistance and a large spiral smoothing flute.
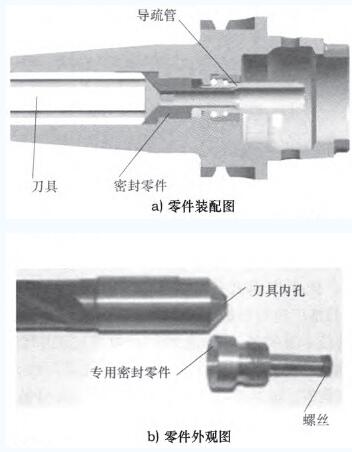
Figure 3 knife assist structure
Figure 3 shows the structure of the knife aid. As can be seen from Fig. 3a, the tail of the tool is an outer tapered surface. When installed, it is used together with a special inner cone sealing ring to reduce the passage dead zone and enhance the passage of the oil mist mixture. As shown in Fig. 3b, the special sealing parts are threaded and shank. Connected and threaded to the plastic sealing draft tube with a small cross-section inside L to ensure that the oil-air mixture passes and reaches the inner cooling hole on the conical surface of the tool that mates with the sealing part. In particular, the deep oil hole processing tool is a coated hard alloy twisted deep hole drill with internal cooling, as shown in Figure 4, which has two inner cooling holes. 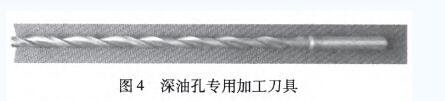
3. After the actual use verification, MQL technology realizes environmental protection processing, and improves the processing quality, especially the tool life. Table 2 shows the comparison of the old and new tool life. Table 3 shows the gun drilling process configuration and cutting. The parameters, as shown in Table 2 and Table 3, greatly reduce the tool usage cost after the actual cutting tool life comparison.
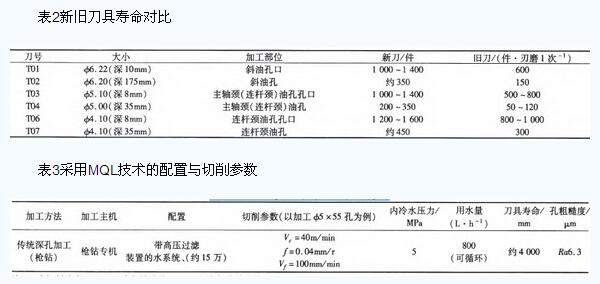
The subsequent technical development is that the lubrication of the electric spindle bearings on the high-speed PM500 horizontal machining center can be lubricated with grease lubrication and oil mist, but the effect is not ideal. Can it share some equipment with MQL technology to realize timing and quantitative oil and gas lubrication? . According to the oil demand of the electric spindle at the lubrication point and the preset working procedure, finally through the distribution of the oil and gas distributor, finally, an extremely fine continuous oil droplet flow is injected into the lubrication points in the electric spindle.
Commercial Street Light,Solar Led Garden Street Lamp,Modern Waterproof Street Light,Ac Integrated Garden Light
Jiangsu chuanglv Transportation Facilities Co., Ltd , https://www.clsolarlights.com